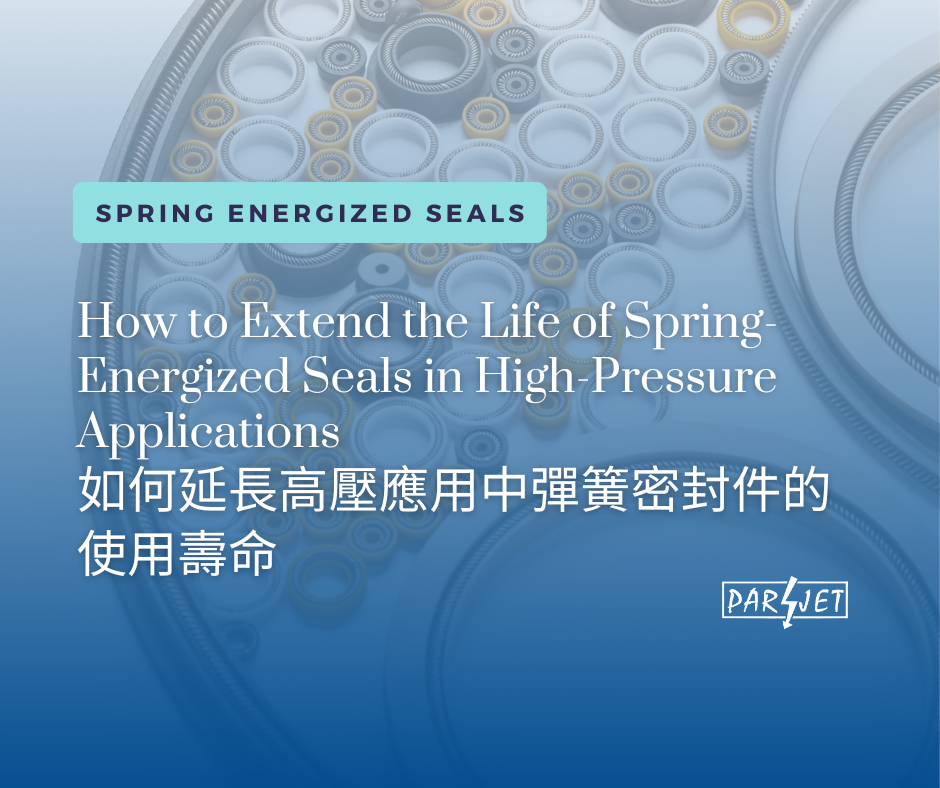
How to Extend the Life of Spring-Energized Seals in High-Pressure Applications
In a highly innovative era, industries are pushing for greater productivity, efficiency, output and quality which requires equipment to operate at higher speed, temperatures and pressure. This led to extreme operating conditions for sealing components. Extending the life of seals became a crucial part. To prolong the usage of spring energized seals (also known as spring loaded seal) in high-pressure applications requires attention to material selection, installation techniques, operating conditions, and maintenance practices. Here’s a comprehensive guide to help improve the longevity of these critical components:
1. Select the Right Materials
- • Jacket Material: Choose a material that withstands the high-pressure environment and resists wear, temperature extremes, and chemical exposure. Some materials can also be combined with additional fillers to enhance the overall performance. Common options include:
• PTFE (Polytetrafluoroethylene): Excellent for high temperatures, chemical resistance, and low friction.
• PEEK (Polyetheretherketone): Good for extreme pressures and temperatures.
• UHMWPE (Ultra-high-molecular-weight polyethylene): Great abrasion resistance.
- Spring Material: Select a spring material that complements the jacket, such as:
• Stainless Steel: Common and corrosion resistant.
• Inconel: Withstands extreme temperatures and corrosive environments.
• Elgiloy: High strength and corrosion resistance.
• Hastelloy: Great for cryogenic or low temperature conditions
2. Ensure Proper Installation
• Inspect Sealing Surfaces: Confirm that the surfaces are clean, smooth, and free from imperfections. Surface roughness can cause rapid wear or create leak paths.
• Avoid Overstretching or Overcompressing: During installation, follow guidelines for fitting to avoid deforming the seal. Overstretching or compressing can have a serious impact on the seal and lead to early failure.
• Lubrication: Apply compatible lubrication during installation to minimize friction and prevent premature wear on the sealing edge.
3. Optimize Seal Design for Application
• Back-Up Rings: Use back-up rings to support the seal in extreme pressures. These rings help prevent extrusion (when the seal is forced into the gap between components), which is a common failure mode at high pressures.
• Choose Appropriate Spring Type: Some applications benefit from a specific spring type. For instance, a helical spring can provide greater sealing force in high-pressure conditions, while a canted coil spring can offer flexibility where variable pressures are present.
• Choose the correct design configuration: There are designs specifically to withstand high pressure conditions, such as extended heels. With the ideal design, spring loaded seals will be able to with higher pressure.
4. Implement a Regular Maintenance Schedule
• Routine Inspections: Check seals regularly for signs of wear, deformation, or leakage. Early identification of issues can prevent failure and prolong the seal’s life.
• Replace Seals Before Full Failure: If seals are showing signs of wear, replace them preemptively to prevent unplanned downtime and potential equipment damage.
• Monitor Operating Conditions: Keep track of temperature, pressure, and fluid compatibility over time, as operating conditions can drift and may require adjustments.
5. Consider Using Double Seals in Extreme Conditions
• In very demanding environments, using a double-seal configuration can provide a backup in case the primary seal starts to fail. This is often used in high-pressure or critical applications where leaks cannot be tolerated.
By implementing these strategies, you can significantly extend the life of spring-energized seals in high-pressure applications, ensuring reliable performance and reducing maintenance costs over time.
At Parjet
Our professional engineering team can provide sealing design consultation for harsh environments. For any design related issues, please contact us here, our team will be happy to advise you on the most demanding operating conditions.