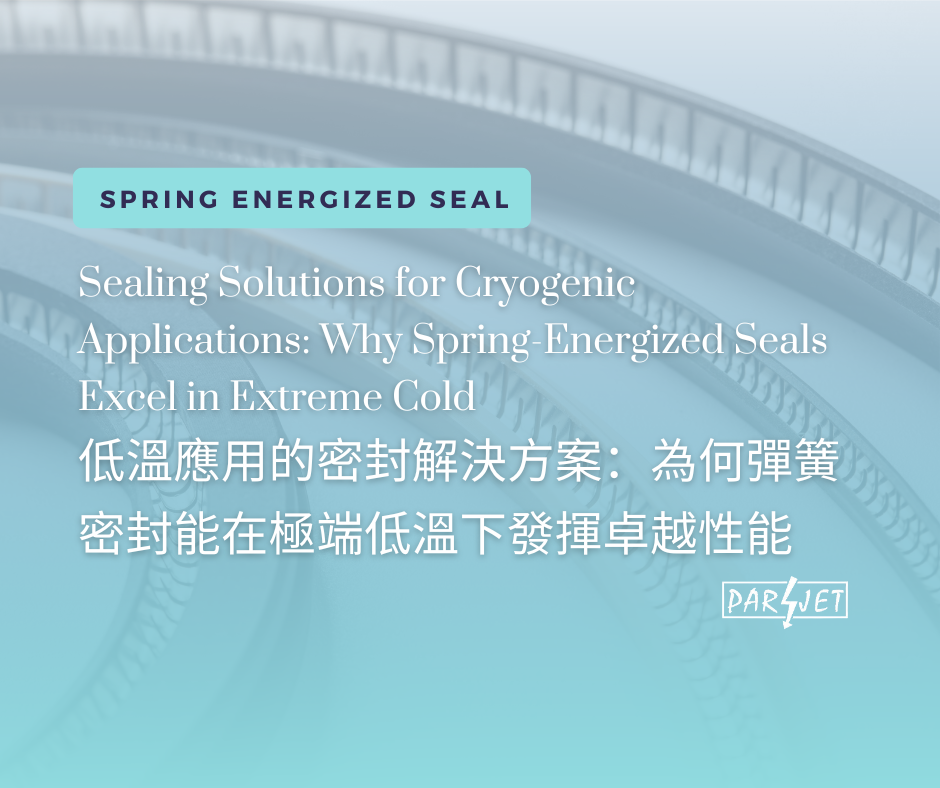
Sealing Solutions for Cryogenic Applications: Why Spring-Energized Seals Excel in Extreme Cold
Sealing in cryogenic environments presents a unique challenge. Traditional seals often fail when exposed to extremely low temperatures, leading to leakage, equipment failure, and safety risks. Spring-energized seals, however, have emerged as the gold standard for maintaining reliable performance in LNG (liquefied natural gas) processing, aerospace, medical, and industrial gas applications. But why do spring-energized seals outperform other sealing technologies in cryogenic conditions? Let’s explore.
The Challenges of Cryogenic Sealing
Cryogenic applications involve temperatures ranging from -150°C to as low as -269°C, where materials behave unpredictably. Here are the key challenges:
• Material Contraction & Shrinkage
At extremely low temperatures, most materials contract significantly, which can cause seal failure due to loss of compression.
• Brittle Fracture
Many conventional elastomers and plastics become brittle and crack in cryogenic conditions, leading to premature seal failure.
• Permeation & Leakage
Cryogenic fluids like liquid oxygen (LOX), nitrogen, and hydrogen can permeate seal materials, creating leak paths and safety hazards.
Why Spring-Energized Seals Excel in Cryogenic Conditions
Unlike traditional O-rings or gaskets, spring-energized seals use a high-performance polymer jacket, usually PTFE compound with a spring energizer (canted coil spring, helical spring and cantilever spring) that maintains contact pressure, ensuring a leak-tight seal even as materials contract.
1. Self-Compensating Design
Thanks to the spring energizer, the spring-energized seals can compensate the seal's dimensional changes due to extreme cold, preventing leaks caused by material shrinkage.
2. Use of Cryogenic-Grade Polymers
Advanced materials like PTFE (Polytetrafluoroethylene), PCTFE (Polychlorotrifluoroethylene), and UHMWPE (Ultra-High Molecular Weight Polyethylene) offer exceptional low-temperature flexibility and chemical resistance.
3. Resistance to Brittleness & Fracture
Unlike elastomers, which can become brittle, PTFE-based spring-energized seals maintain mechanical integrity at cryogenic temperatures.
4. Chemical Compatibility & Purity
Cryogenic applications often involve liquid oxygen, liquid nitrogen, and hydrogen, which require materials with low outgassing and non-reactive properties. PTFE and PCTFE excel in these conditions.
5. Low Friction & Wear Resistance
Spring-energized seals have low friction, making them ideal for dynamic applications such as cryogenic valves, pumps, and rotating equipment.
Applications of Spring-Energized Seals in Cryogenic Industries
• Aerospace & Space Exploration – Used in rocket propulsion systems and fuel transfer lines for liquid hydrogen and oxygen storage.
• Industrial Gas & LNG Processing – Ensures leak-free operation in liquid nitrogen, helium, and LNG transfer systems.
• Medical & Pharmaceutical Equipment – Critical for MRI machines, cryopreservation, and medical gas systems.
• Scientific & Research Labs – Used in cryostats and superconducting applications for particle accelerators and quantum computing.
Future Innovations in Cryogenic Sealing
As demand for clean energy, space exploration, and advanced medical technologies grows, sealing technology must evolve:
• Enhanced polymer formulations for even lower permeability and higher durability
• Nano-engineered surface treatments to further reduce friction and wear
• AI-driven predictive maintenance to monitor seal performance in real-time
Conclusion
Spring-energized seals have proven to be the most reliable sealing solution for cryogenic applications due to their self-adjusting design, material resilience, and superior sealing performance at ultra-low temperatures. As industries push the boundaries of cryogenic engineering, advancements in sealing technology will continue to play a crucial role in safety, efficiency, and performance.
Contact us now to get more information on Spring Energized Seals - HiPerSeal®